Introduction
Magnets are fundamental components in numerous industries, powering everything from simple refrigerator magnets to advanced medical and aerospace technologies. However, not all magnets are created equal. The differences between regular magnets and neodymium magnets lie in their composition, strength, durability, and applications. Understanding these distinctions is crucial when selecting the correct type of magnet for a specific function.
Understanding Magnetic Materials: Why the Type of Magnet Matters
Magnets operate based on the principles of magnetism, a force generated by the alignment of atomic structures within ferromagnetic materials. The type of magnet used significantly impacts performance, efficiency, and longevity. Whether in industrial machinery or consumer electronics, selecting the appropriate magnet can optimize operational outcomes and reduce maintenance costs.
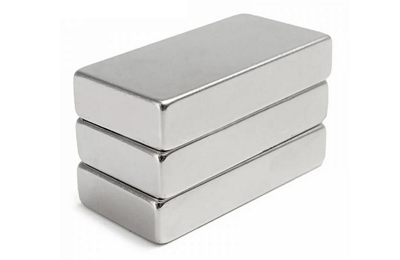
Neodymium Magnets
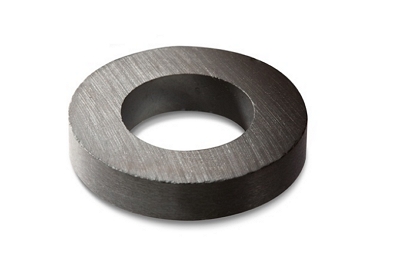
Ferrite Magnets
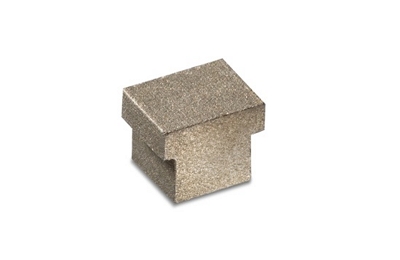
Samarium Cobalt Magnets
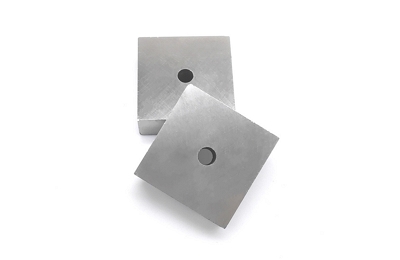
Alnico Magnets
The Role of Magnets in Everyday Life and Industrial Applications
Magnets are ubiquitous in modern society. In everyday applications, they are found in household items such as speakers, electric motors, and door latches. In industrial settings, they play a pivotal role in wind turbines, medical imaging devices, and precision engineering. Understanding the differences between regular and neodymium magnets ensures that industries can maximize efficiency and longevity in their applications.
Basics of Regular Magnets and Neodymium Magnets
What Are Regular Magnets? Common Types and Composition
Regular magnets, also known as conventional magnets, include ferrite (ceramic), alnico, and samarium-cobalt magnets. These magnets are composed primarily of iron and other common elements. Ferrite magnets, for instance, are made from iron oxide combined with barium or strontium, making them cost-effective and widely available. Alnico magnets, an alloy of aluminum, nickel, and cobalt, offer superior temperature resistance but lower magnetic strength compared to neodymium magnets.
What Are Neodymium Magnets? The Science Behind Their Strength
Neodymium magnets belong to the rare-earth magnet family, consisting of neodymium, iron, and boron (NdFeB). Their exceptional strength results from the unique arrangement of atoms in their crystalline structure, allowing them to generate intense magnetic fields. Neodymium magnets can hold significantly more weight than traditional magnets of the same size, making them indispensable in high-performance applications.
Manufacturing Process: How Regular and Neodymium Magnets Are Made
Regular magnets, such as ferrite magnets, are produced by sintering or compression molding a mixture of iron oxide and other elements. The manufacturing process is relatively simple, contributing to their low cost.
In contrast, neodymium magnets undergo a more intricate production process. The raw materials are melted and rapidly cooled to form a fine powder. This powder is then pressed into shape and sintered at high temperatures before being coated to prevent corrosion. The final product exhibits superior strength and durability compared to regular magnets.
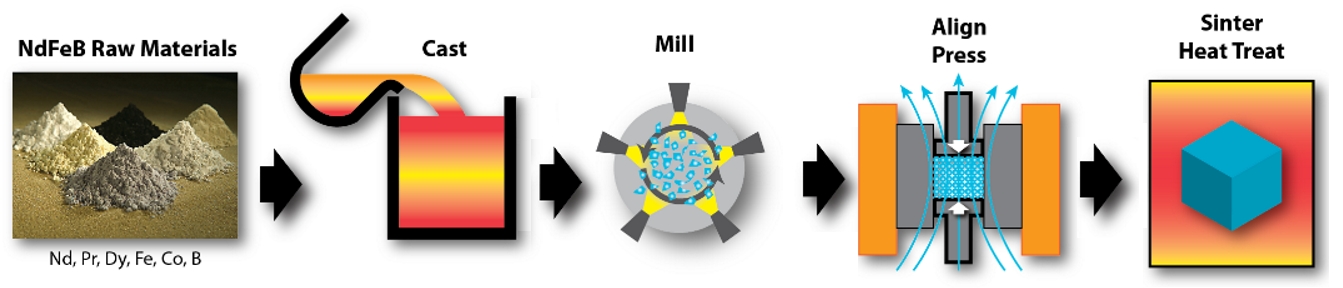
Magnetic Strength and Performance
Why Neodymium Magnets Are the Strongest: A Look at Magnetic Properties
Neodymium magnets possess the highest energy product (BHmax) among commercially available magnets. Their strong internal magnetic alignment, due to their unique crystalline structure, allows them to produce powerful magnetic fields while maintaining a compact size.
Comparing Magnetic Field Strength: How Regular Magnets Stack Up
Regular magnets, while effective for various applications, do not compare in strength to neodymium magnets. Ferrite magnets, for example, have a lower magnetic field density and are less effective in high-performance applications where stronger forces are required.
Retaining Magnetism: Differences in Durability and Demagnetization Resistance
Alnico and ferrite magnets exhibit high resistance to demagnetization due to their stable atomic structures. However, they are weaker in comparison. Neodymium magnets, despite their strength, can be susceptible to demagnetization if exposed to high temperatures unless specifically designed with heat-resistant coatings or additives.
Material Composition and Durability
Regular Magnets: Iron, Ferrite, and Alnico Explained
Regular magnets primarily rely on iron-based compositions. Ferrite magnets contain iron oxide, whereas alnico magnets are a blend of aluminum, nickel, and cobalt. Each type offers distinct advantages, such as corrosion resistance (ferrite) and thermal stability (alnico).
Neodymium Magnets: The Rare Earth Element Advantage
Neodymium magnets derive their strength from rare-earth elements, particularly neodymium and dysprosium. These elements enable an extremely high energy density, making neodymium magnets superior in terms of strength-to-weight ratio.
Resistance to Corrosion and Wear: Which Magnet Lasts Longer?
Ferrite magnets are naturally corrosion-resistant due to their ceramic-like composition. Neodymium magnets, however, require protective coatings, such as nickel or epoxy, to prevent oxidation. Without this protective layer, neodymium magnets can deteriorate when exposed to moisture.
Applications and Use Cases
Everyday Uses of Regular Magnets: Where They Are Commonly Found
Regular magnets are used in low-cost consumer goods such as refrigerator magnets, door catches, and simple motors. They are effective for applications where extreme strength is not required.
High-Tech and Industrial Applications of Neodymium Magnets
Neodymium magnets are integral to advanced technologies. They are used in electric vehicle motors, hard disk drives, MRI machines, and wind turbines. Their superior strength makes them essential in aerospace and robotics applications where compact and powerful magnets are necessary.
Safety Considerations: Handling and Storing Neodymium Magnets
Due to their intense magnetic pull, neodymium magnets can pose serious safety risks. They can attract metal objects with great force, causing injuries if mishandled. Proper storage and handling procedures, such as keeping them away from electronic devices and medical implants, are crucial to prevent accidents.
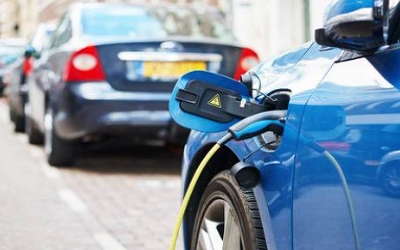
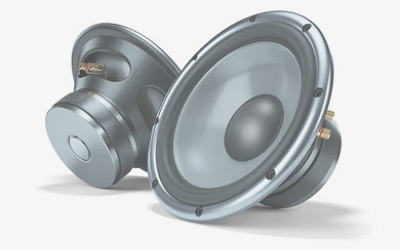
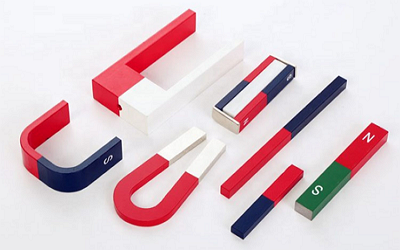
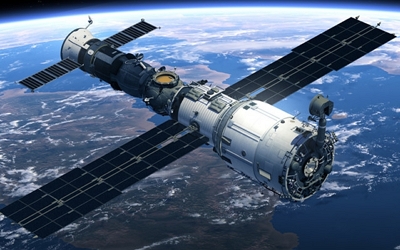
Cost and Availability
The Price Factor: Why Neodymium Magnets Are More Expensive
Neodymium magnets are significantly more expensive due to their reliance on rare-earth elements, which require complex extraction and refinement processes. Additionally, their intricate manufacturing process adds to the overall cost.
Global Supply and Production: Availability of Regular vs. Neodymium Magnets
Regular magnets are widely available and manufactured in bulk due to their reliance on common materials like iron oxide. Neodymium magnets, on the other hand, face supply constraints as rare-earth elements are predominantly mined in select regions, such as China, leading to price volatility.
Environmental Impact and Sustainability
Mining and Production: Environmental Considerations for Each Type
The production of ferrite magnets has a relatively low environmental impact compared to neodymium magnets. Rare-earth element extraction involves extensive mining operations, which generate hazardous waste and environmental degradation.
Recycling and Disposal: Challenges and Best Practices
Recycling neodymium magnets remains a challenge due to the difficulty of separating rare-earth elements from other materials. However, efforts are underway to develop efficient recycling methods to reduce dependency on new mining operations. Ferrite magnets, on the other hand, can be more easily recycled due to their more straightforward composition.
Conclusion
Choosing the Right Magnet for the Job: Key Takeaways
Selecting the appropriate magnet depends on the application. Regular magnets are cost-effective and suitable for low-performance tasks, while neodymium magnets offer superior strength and are ideal for high-tech applications requiring compact, robust solutions.
Future Trends in Magnet Technology and Material Innovation
As demand for high-performance magnets continues to rise, researchers are exploring new materials and manufacturing techniques to improve efficiency and sustainability. Advancements in rare-earth recycling, high-temperature neodymium magnets, and alternative magnetic materials will shape the future of magnetic technology.
Post time: Mar-03-2025