From smartphones and wireless earbuds to electric vehicles, the driving force behind countless modern innovations lies in a hidden hero: sintered neodymium iron boron (NdFeB) magnets. These high-performance permanent magnets owe their exceptional magnetic properties to a critical manufacturing step - sintering. This article delves into the pre-sintering process of NdFeB magnets, unravelling how raw materials transform into the backbone of cutting-edge technologies.
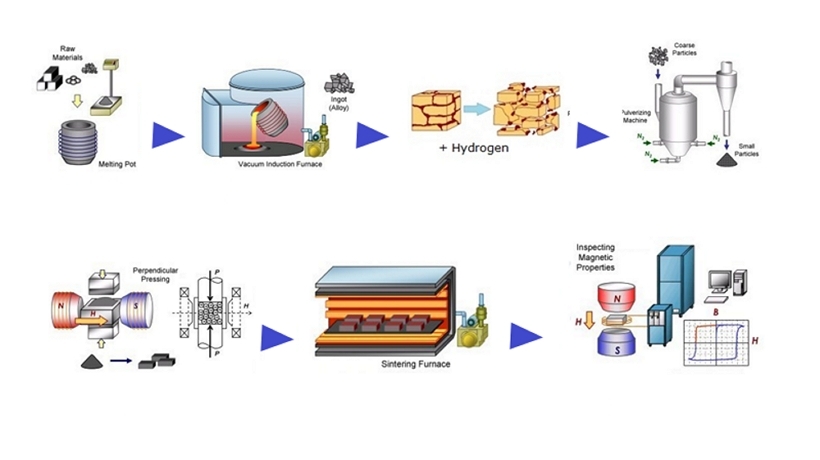
What is Sintering?
Sintering is a material fabrication technique that bonds powdered substances into dense, solid structures through controlled heat and pressure. Imagine baking ceramics: loose clay particles fuse under high temperatures to form a rigid, cohesive structure. Similarly, sintering enables metal or ceramic powders to coalesce at atomic levels, creating materials with enhanced mechanical and magnetic properties.
Key Insight: Sintering is not merely heating - it’s a strategic orchestration of temperature, time, and atmosphere to optimize atomic diffusion and grain bonding.
Why Sintering is Essential for NdFeB Magnets?
NdFeB magnets, composed primarily of neodymium (Nd), iron (Fe), and boron (B), boast extraordinary magnetic properties - high remanence (Br), coercivity (Hcb), and energy product (BHmax). These qualities make them indispensable in modern technology. However, their complex composition and crystalline structure pose unique manufacturing challenges. Traditional methods like casting or forging fall short, as they can’t achieve the precision and performance required.
Sintering, paired with powder metallurgy, offers the perfect solution. By breaking the process into manageable stages—starting with raw materials and ending with a fully formed magnet - sintering ensures that NdFeB magnets achieve their optimal magnetic potential. It’s the cornerstone of their production, bridging the gap between raw ingredients and finished products.
The Pre-Sintering Process: Step-by-Step
The journey to create an NdFeB magnet begins long before the sintering furnace fires up. The pre-sintering stages—melting, milling, and shaping—are critical to preparing the material for its final transformation. Let’s break it down step by step.
1. Melting: Crafting the Perfect Alloy
The process starts with precision. Raw materials—neodymium, iron, boron, and trace amounts of elements like dysprosium (Dy), niobium (Nb), or copper (Cu)—are carefully measured and blended. The typical composition is roughly 29-32.5% neodymium, 63.95-68.65% iron, and 1.1-1.2% boron, with minor additions to enhance performance.
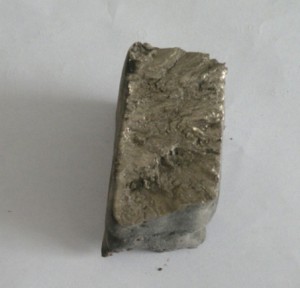
Pr-Nd
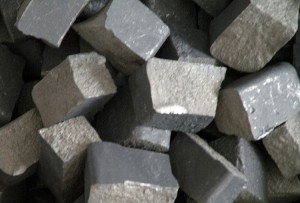
Dy-Fe
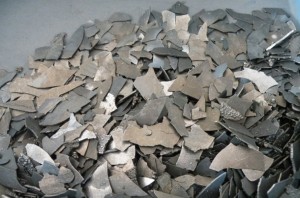
Co
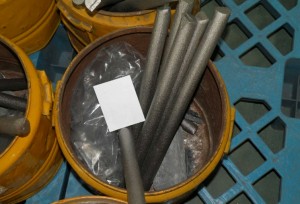
Fe
These materials are then melted in a vacuum induction furnace at temperatures between 1400-1550°C. The vacuum environment prevents contamination from oxygen or other impurities, ensuring a pure alloy. Once molten, the liquid alloy is poured onto a rapidly spinning copper roller, cooling it into thin flakes (0.2-0.45 mm thick) at a casting temperature of 1380-1510°C. This rapid solidification creates a uniform crystalline structure, laying the groundwork for the next stage.
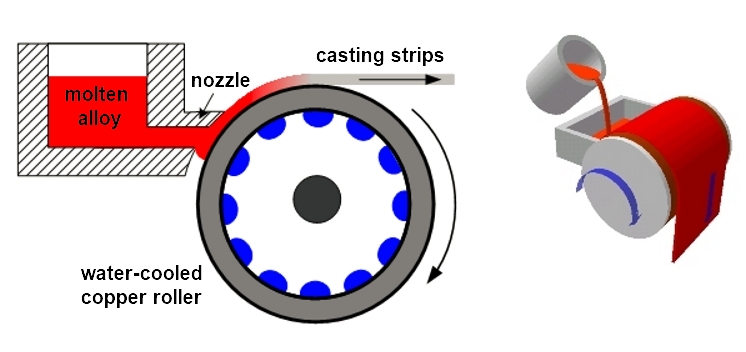
Method of Melting
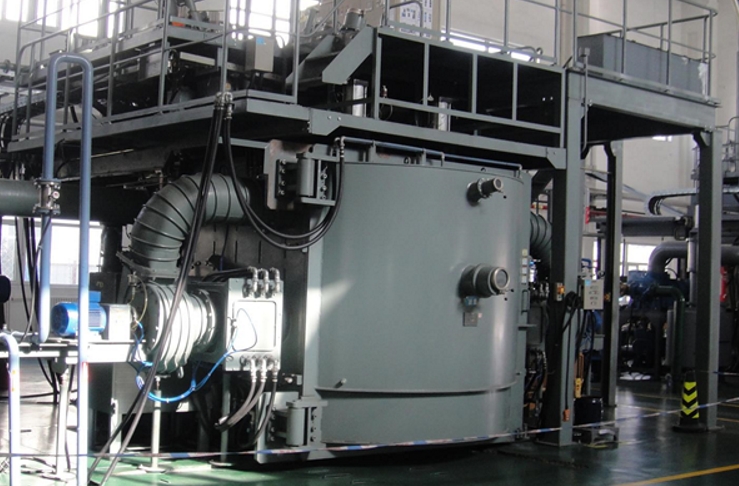
Vacuum Furnace
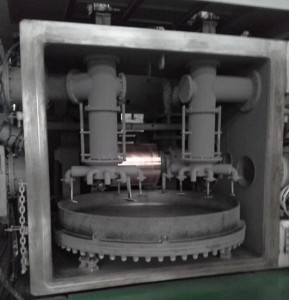
Inside Vacuum Furnace
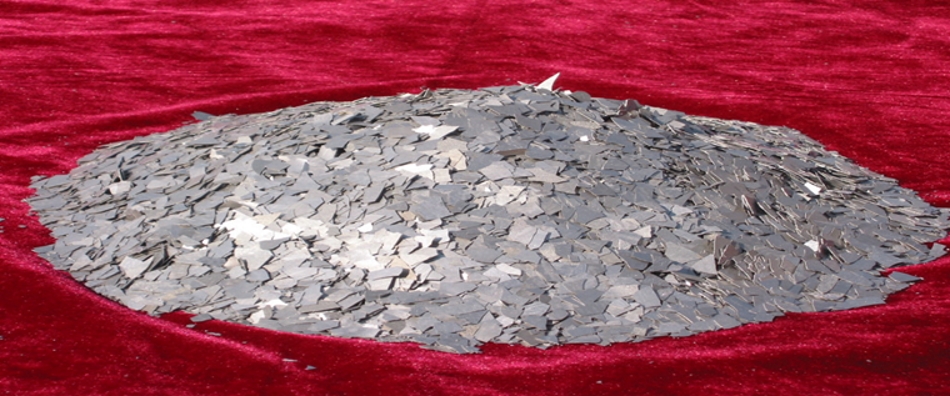
Casting Strips
2. Milling: Turning Flakes into Fine Powder
Next, the alloy flakes are transformed into fine powder—a critical step for achieving the magnet’s final properties. This milling process happens in two phases:
• Hydrogen Decrepitation (HD): This ingenious technique uses hydrogen gas to break down the flakes. The alloy absorbs hydrogen, causing it to expand and fracture along its neodymium-rich phases. The result? Coarse powder ready for further refinement. HD is efficient and produces smaller, more uniform grains (typically <10 μm), boosting coercivity and corrosion resistance compared to traditional mechanical crushing.
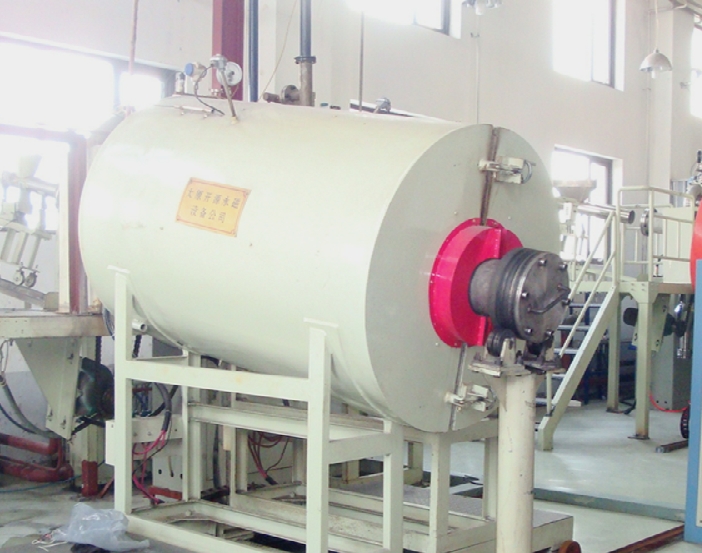
Hydrogen Decrepitation Furnace
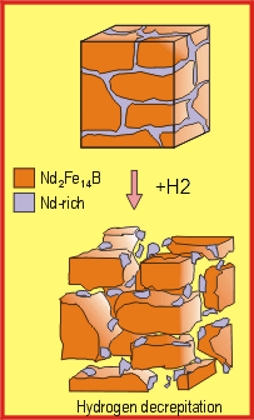
HD Method
• Jet Milling: The coarse powder is then fed into a jet mill, where high-pressure gas streams propel particles into high-speed collisions. This grinds the powder down to a fine size, usually 2.8-3.5 μm, with a uniform distribution. The finer the powder, the better the magnetic properties—but it also increases the risk of oxidation, so a small amount of air is introduced to passivate the particles.
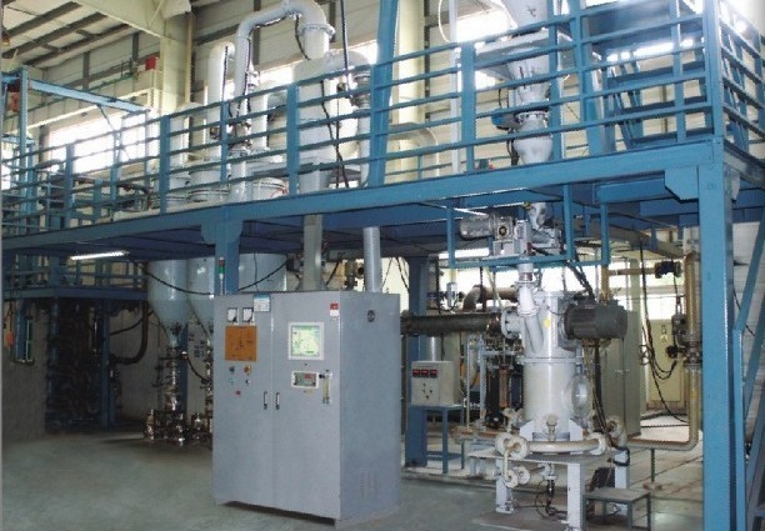
Jet Milling Machine
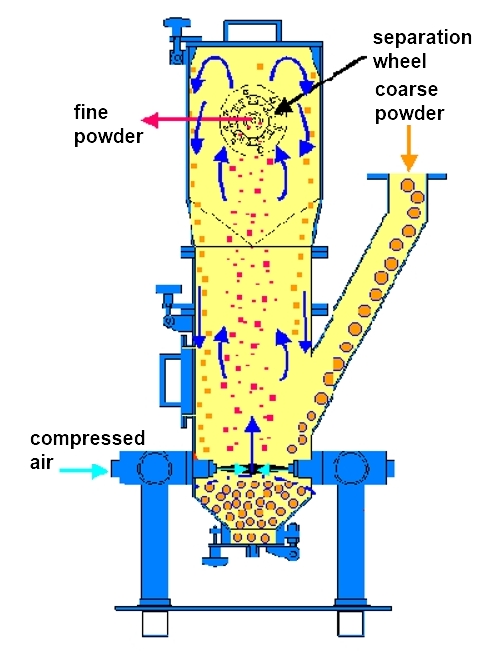
Jet Milling Method
3. Pressing: Forming the Magnet Blank
With the powder prepared, it’s time to give the magnet its shape. This stage involves pressing the powder into a compact form, or “green compact,” using molds tailored to the desired geometry—cylinders, cubes, tiles, or rings, depending on the application.
• Magnetic Field Pressing: The powder is pressed under a magnetic field to align the particles’ magnetic domains. This alignment is crucial for maximizing the magnet’s strength. The pressure compacts the powder into a fragile blank with a density of about 4.0-4.2 g/cm³.
• Isostatic Pressing: For even more excellent uniformity, the blank undergoes isostatic pressing. Submerged in hydraulic oil, it’s subjected to omnidirectional pressure, boosting its density to 4.5-4.9 g/cm³. This step ensures the blank is robust and evenly packed, ready for sintering.

Pressing Machine
4. Sintering: Setting the Stage for Sintering
By the end of the pre-sintering process, the NdFeB blank had taken shape, but it was still a fragile, porous structure with untapped potential. The next step—sintering—will heat it to 1050-1150°C in a vacuum furnace, fusing the particles into a dense, high-performance magnet. This is followed by aging (500-900°C) to refine its microstructure and enhance coercivity.
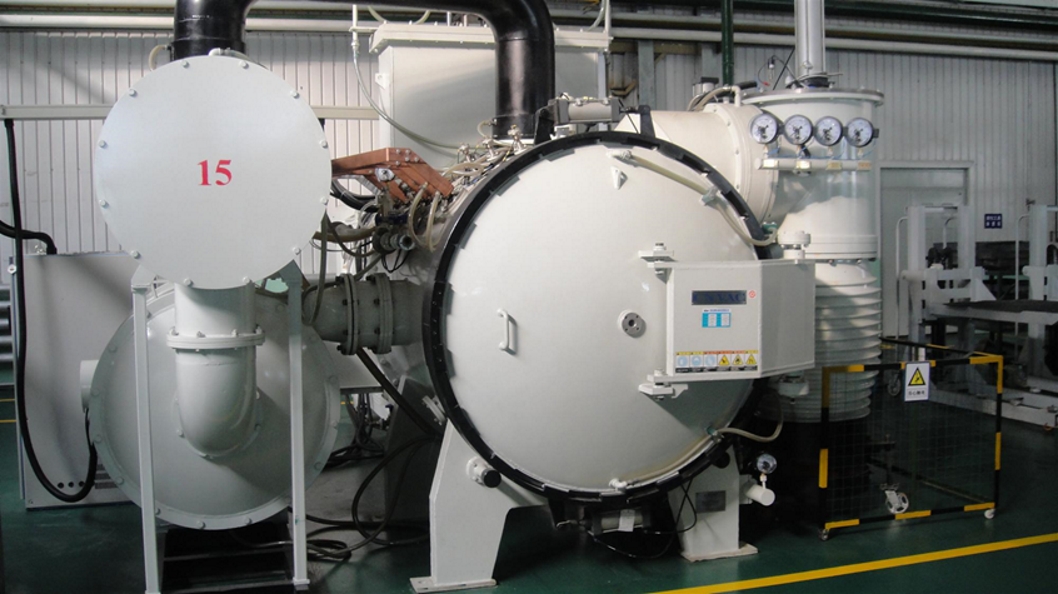
Vacuum Sintering Furnace
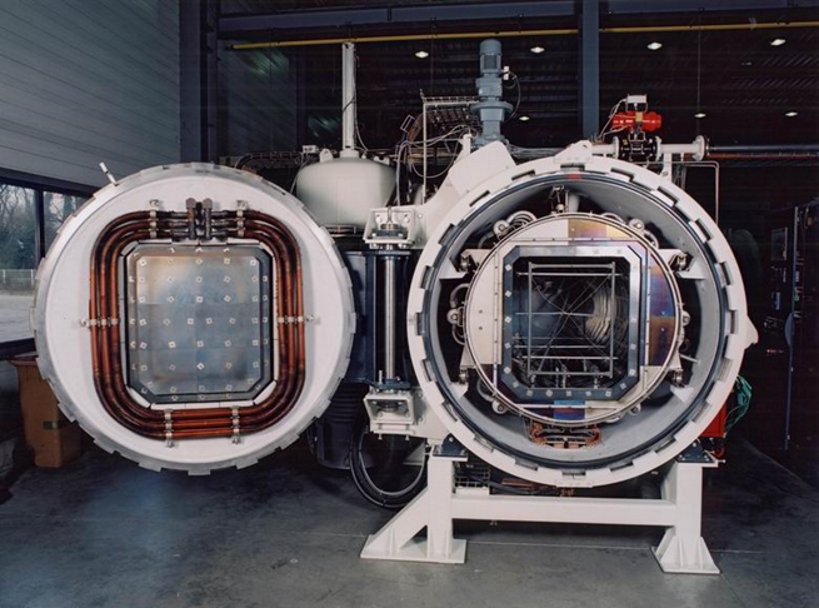
Inside Sintering Furnace
Together, these pre-sintering stages—melting, milling, and pressing—form the foundation of NdFeB magnet production. Each step is a delicate balance of science and engineering, ensuring the raw materials evolve into a blank ready to unleash its magnetic power.
Quality Assurance: Ensuring Excellence
Every sintered blank undergoes rigorous testing:
• Dimensional Accuracy: Measured via CMM (Coordinate Measuring Machine).
• Density: Evaluated using Archimedes’ principle.
• Magnetic Properties: Tested with BH analyzers to verify Br, Hcj, and (BH)max.
• Microstructural Analysis: SEM/TEM imaging assesses grain size and phase distribution.
• Environmental Durability: Salt spray and thermal cycling tests validate corrosion and temperature resistance.
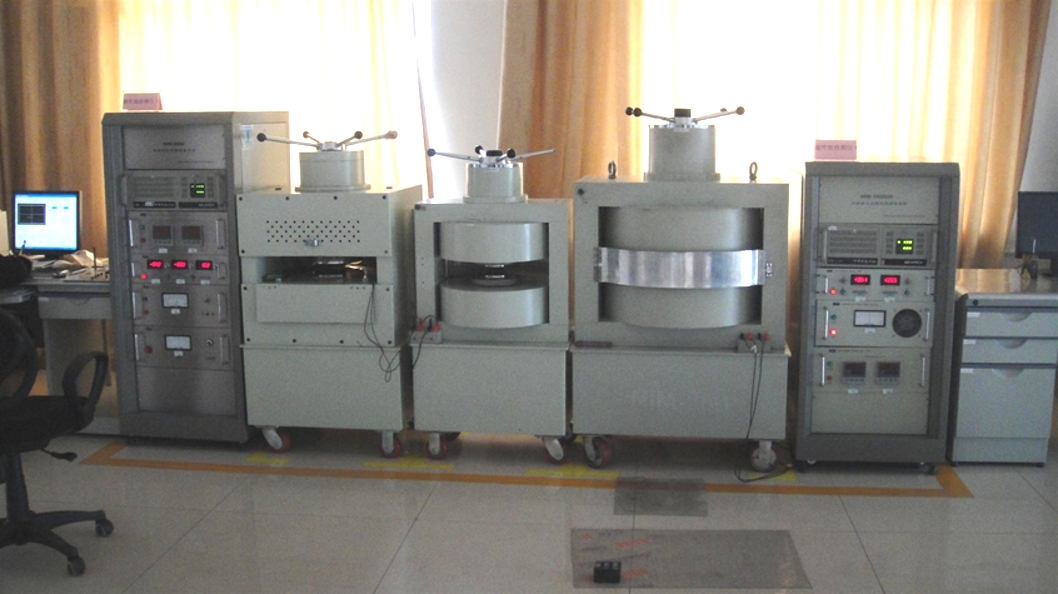
Hysteresis Loop Tracers
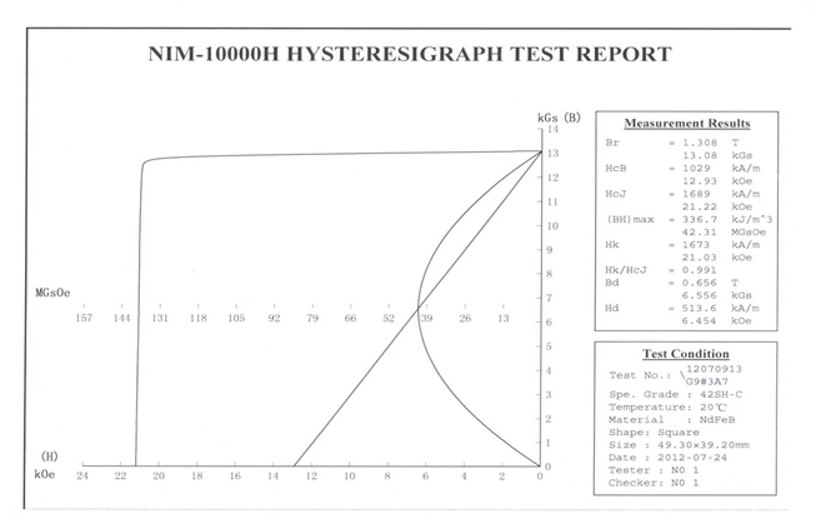
Hysteresis Loop
The pre-sintering process isn’t without its hurdles. Precise control of powder size, oxygen levels, and pressing conditions is essential to avoid defects like porosity or uneven density. Advances like hydrogen decrepitation and jet milling have improved efficiency and quality, while ongoing research explores ways to reduce rare-earth content without sacrificing performance—a nod to sustainability in magnet production.
The pre-sintering process of NdFeB magnets is a testament to the ingenuity behind modern materials science. From molten alloy to finely shaped blanks, each stage builds toward the creation of magnets that power our world. Whether you’re a tech enthusiast or an industry professional, understanding this process reveals the hidden craftsmanship behind everyday innovations.
At AIC Magnetics, we combine decades of expertise in magnetic materials with state-of-the-art sintering technology to deliver NdFeB solutions tailored to your needs. Contact us to explore how our magnets can drive your next breakthrough.
Post time: Feb-27-2025