Magnets are fundamental components in countless technologies we use every day. Sintered Neodymium Iron Bore (NdFeB) magnets stand out as the most powerful type commercially available. NdFeB magnets are a cornerstone of modern engineering, and in this blog, we'll explore why.
1. What are Sintered NdFeB Magnets?
A Tale of Two Inventors
The story of NdFeB magnets began in 1983 with independent inventions by Masato Sagawa at Sumitomo Special Metals in Japan (now Hitachi Metals) and General Motors in the United States. These simultaneous breakthroughs led to the third generation of permanent magnets, and NdFeB remains largely unrivaled in magnetic strength today.
The Recipe for Magnetic Power
The chemical formula for NdFeB is Nd2Fe14B. Think of it as a precise recipe:
• Neodymium (Nd) (around 30% by weight): The key ingredient, a rare earth element that provides the core magnetic properties.
• Iron (Fe) (around 60% by weight): The workhorse element, contributing to the magnetic strength and structural integrity.
• Boron (B) (around 1% by weight): Essential for forming the unique crystal structure that enables high performance.
• Dysprosium (Dy) & other additives (1-5% total): Like spices in a dish, small amounts of elements like Dysprosium (Dy), Terbium (Tb), Praseodymium (Pr), Cerium (Ce), Aluminum (Al), Copper (Cu), Cobalt (Co), and Niobium (Nb) are added to fine-tune the magnet's properties. These additions can enhance magnetic performance, improve temperature stability, or reduce cost depending on the desired grade.
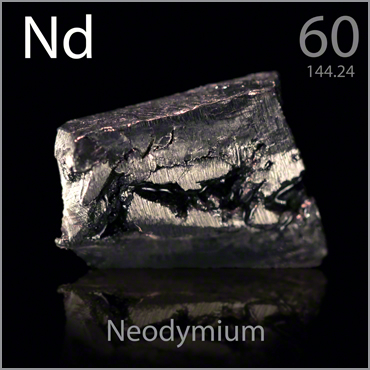
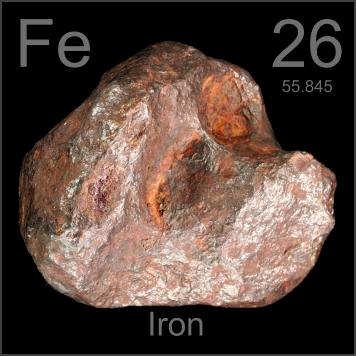
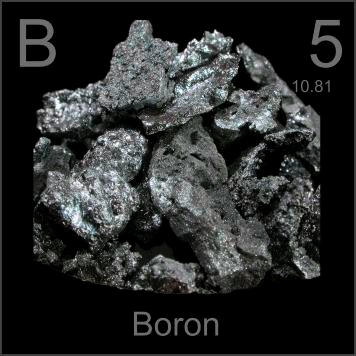
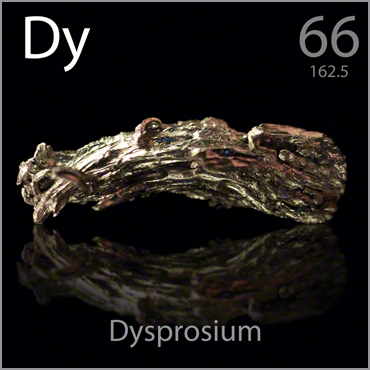
Decoding the Grades
NdFeB magnets are categorized by grades, indicated by a combination of letters and numbers.
• Numbers (e.g., 35, 40, 52): These roughly correspond to the Maximum Energy Product ((BH)max), a key measure of magnet strength. Higher numbers mean stronger magnets.
• Letters (N, M, H, SH, UH, EH, AH) denote the Intrinsic Coercivity (Hcj), indicating the magnet's resistance to demagnetization. Higher letters (further along in the alphabet) signify higher coercivity and better performance at elevated temperatures. For example:
N: Normal Coercivity, Hcj ≥ 955 kA/m (12 kOe) (e.g., N40) - General purpose applications.
M: Medium Coercivity, Hcj ≥ 1114 kA/m (14 kOe) (e.g., 48M) - Improved temperature performance compared to N grades.
H: High Coercivity, Hcj ≥ 1353 kA/m (17 kOe) (e.g., 45H) - For higher temperature environments.
SH: Super High Coercivity, Hcj ≥ 1592 kA/m (20 kOe) (e.g., 42SH) - Suitable for demanding thermal conditions.
UH: Ultra High Coercivity, Hcj ≥ 1990 kA/m (25 kOe) (e.g., 38UH) - For very high operating temperatures.
EH: Extra High Coercivity, Hcj ≥ 2388 kA/m (30 kOe) (e.g., 35EH) - Extreme temperature resistance.
AH: Extreme High Coercivity, Hcj ≥ 2624 kA/m (33 kOe) (e.g., 28AH) - Ultra-high temperature applications.
Currently, the highest commercially available grades boast a Maximum Energy Product exceeding 440 kJ/m³ (around 55 MGOe). The theoretical limit is even higher! They can achieve Remanence (Br) up to 1.5 Tesla and Coercivity (Hcj) over 2500 kA/m (30 kOe). A small NdFeB magnet can lift hundreds of times its weight!
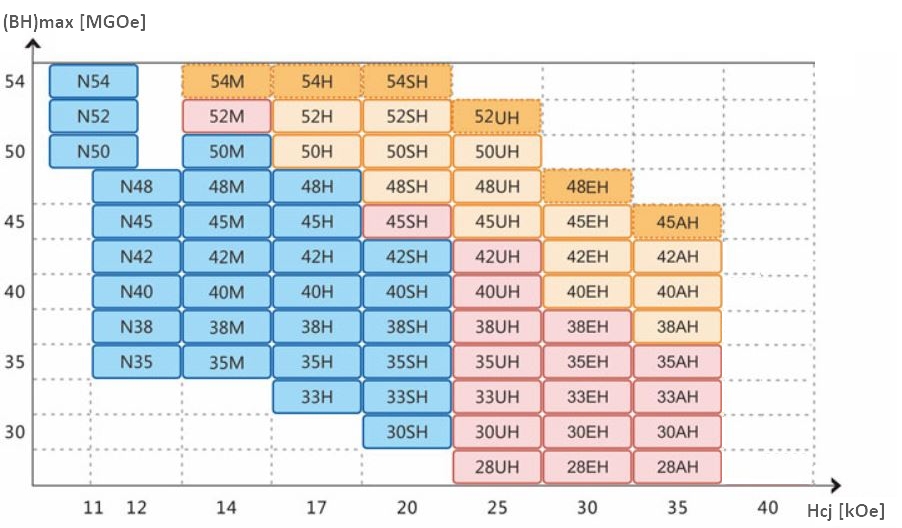
Trade-offs: Temperature Sensitivity & Corrosion
While incredibly powerful, NdFeB magnets have some limitations:
• Lower Curie Temperature: Their Curie temperature (the point where they lose magnetism) is relatively low (310-410°C), limiting their high-temperature applications. Standard grades typically operate below 80-150°C, though some specialized grades can reach 200°C or higher.
• Corrosion Susceptibility: They are prone to rust and are composed of iron and neodymium. Surface plating (like Nickel, Epoxy, etc.) is essential for protection.
2. The Rise and Reach of NdFeB Magnets
China's Dominance
Fueled by resource availability, cost efficiency, and advancements in manufacturing technology, China has become the world's leading producer of NdFeB magnets. By 2020, China's output reached 186,000 tons, representing over 90% of global production exceeding 200,000 tons.
Applications Across Industries
NdFeB magnets are incredibly versatile, with applications spanning diverse sectors:
• Traditional Applications: Consumer electronics (smartphones, laptops, tablets), industrial motors, audio equipment, magnetic separators, electric bicycles, toys, and more. These sectors represent a stable demand base.
• Emerging "Green" Applications: The most significant growth areas are in renewable energy and energy efficiency, including:
- Wind Turbines: Large NdFeB magnets are crucial for high-efficiency wind generators.
- Electric Vehicle (EV) Motors: NdFeB magnets are essential for robust and efficient motors that drive EVs and hybrid vehicles.
- Industrial Robots & Automation: Enabling precise and robust motion control.
- Energy-Efficient Elevators & HVAC Systems: Contributing to energy savings in buildings.
- High-Speed Rail: Used in advanced traction motors.
- Medical Imaging (MRI): Critical for generating strong and stable magnetic fields.
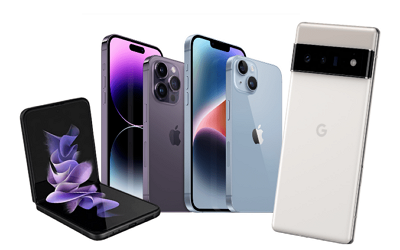
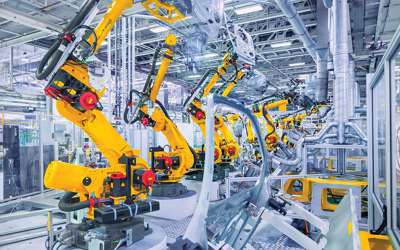
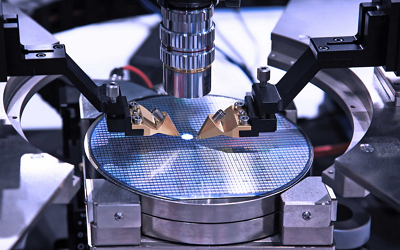
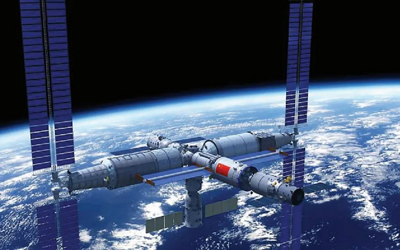
3. Manufacturing NdFeB Magnets
The production of sintered NdFeB magnets involves four main stages:
Stage 1: Sintered Magnet Blanks Production
This stage focuses on creating magnet blanks with the desired shape and magnetic properties. Key steps include:
1. Raw Material Preparation & Batching: Precise weighing and quality control of raw materials (Iron, Neodymium, Ferroboron, Dysprosium, etc.) according to specific formulas.
2. Melting & Strip Casting: Vacuum induction melting and rapid solidification (melt spinning) to create thin alloy ribbons with a fine crystalline structure.
3. Hydrogen Decrepitation (HD) and milling: The alloy ribbons are broken down into coarse powder (HD) and then further milled into ultra-fine powder (jet milling) with an average particle size of around 3µm.
4. Pressing & Alignment: Compressing the powder into desired shapes in molds while applying a magnetic field to align the magnetic particles (die pressing or isostatic pressing).
5. Sintering & Annealing: The pressed compacts are heated in a vacuum furnace to fuse the particles (sintering) and then heat-treated (annealing/tempering) to optimize the microstructure and magnetic properties.
6. Magnet Blanks Inspection: Rigorous inspection of the sintered blanks for dimensions, density, magnetic properties, and surface defect
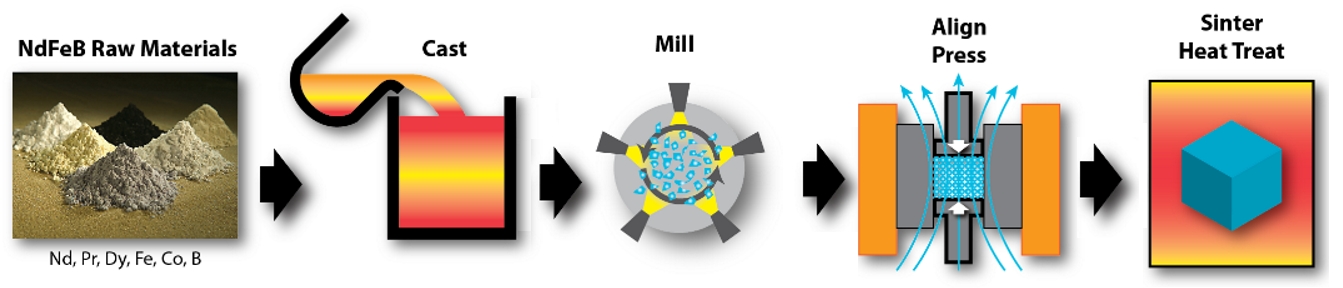
Stage 2: Machining
Sintered NdFeB is hard and brittle, requiring specialized machining techniques to achieve precise final shapes and dimensions based on customer drawings. Common methods include:
• Slicing: Cutting large blocks into smaller pieces, mainly for flat surfaces.
• Wire EDM (Electrical Discharge Machining): For complex curves and large flat areas.
• Surface Grinding: Precision grinding of flat surfaces.
• Profile Grinding: For high-precision curved surfaces.
• Ultrasonic Drilling: Creating small holes.
• Counterboring: Creating larger diameter holes.
• Chamfering: Rounding sharp edges.
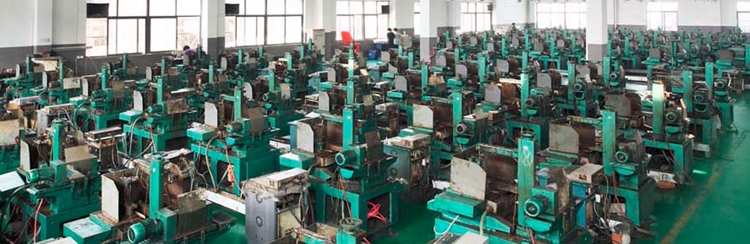
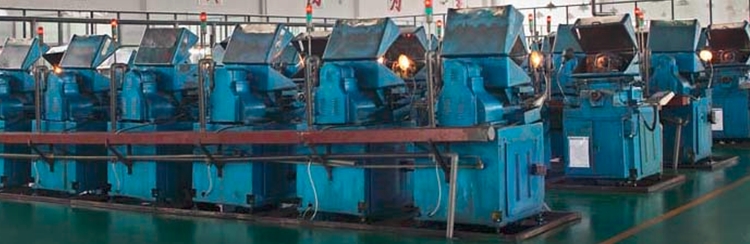
Stage 3: Surface Treatment
Protecting the magnets from corrosion is crucial. Common surface treatments include:
• Nickel Plating (Ni-Cu-Ni): Excellent corrosion resistance, high-temperature stability, and widely used.
• Zinc Plating (Various Finishes): Lower cost, but limited temperature range and corrosion resistance.
• Epoxy Coating (Black or Gray, Electrophoretic or Spray): Organic coating provides good insulation and corrosion protection, especially in humid environments.
• Phosphating/Passivation: Temporary protection between manufacturing steps.
• Tin, Gold, Silver Plating: For specific solderability or conductivity applications.
• PVD (Physical Vapor Deposition) Coatings (e.g., Aluminum): Enhanced hardness and wear resistance.
• CVD (Chemical Vapor Deposition) Coatings (e.g., Parylene): Exceptional corrosion resistance and insulation.
Stage 4: Packaging & Outgoing
Final inspection and packaging to ensure magnets reach customers in perfect condition, with appropriate magnetic shielding for safe transport.
Sintered NdFeB magnets are truly remarkable materials. They power a wide array of modern technologies and drive innovation in critical sectors like renewable energy and transportation. Their exceptional magnetic strength and ongoing advancements in materials science and manufacturing have ensured their continued importance for years.
Post time: Feb-08-2025