Introduction
Magnets are crucial in modern engineering, manufacturing, and consumer applications. However, selecting the right magnet requires more than just choosing a strong one; it demands a deep understanding of magnet grades and performance characteristics. Magnet tables are a vital reference, offering key data points that help engineers, designers, and procurement specialists make informed decisions. This guide explores the significance of magnet grades, how they relate to performance, and the nuances of interpreting magnet tables effectively.
The Importance of Understanding Magnet Grades
Magnet grades provide a standardized way to classify and compare different magnets. These grades indicate critical properties such as strength, coercivity, and temperature resistance. Without this understanding, selecting a magnet becomes a guessing game, potentially leading to suboptimal performance or premature failure in an application.
How Magnet Tables Help in Selecting the Right Magnet
Magnet tables compile essential data for various magnet grades, providing a quick reference for engineers and manufacturers. These tables include key performance metrics such as magnetic flux density, energy product, and thermal thresholds, allowing users to compare different materials and grades to find the most suitable option for their application.
Overview of Key Magnet Performance Factors
Several factors influence magnet performance, each playing a crucial role in determining its suitability for a specific application:
• Magnetic Strength (Br) - Defines the intensity of the magnetic field.
• Coercivity (Hc) - Indicates resistance to demagnetization.
• Maximum Energy Product (BHmax) - Represents overall magnet performance.
• Temperature Stability - Determines operational limits in extreme environments.
Understanding these factors enables precise magnet selection, ensuring long-term efficiency and reliability.
Magnet Grades: What Do They Mean?
The Basics of Magnet Grading: Decoding the Alphanumeric Codes
Magnet grades consist of alphanumeric designations that reflect the intrinsic properties of a magnet. For example, a neodymium magnet labeled N52 signifies a high-performance variant, where "N" represents neodymium, and "52" indicates its maximum energy product (BHmax) in MegaGauss-Oersteds (MGOe). Similarly, other materials follow distinct grading conventions based on their magnetic and thermal properties.
How Grade Numbers Relate to Magnetic Strength and Performance
Higher grade numbers generally indicate stronger magnets, but strength alone isn't the only deciding factor. A high-grade magnet with poor coercivity may be unsuitable for external magnetic interference applications. Understanding the balance between strength, stability, and temperature tolerance is key when interpreting magnet grades.
Variations in Grades Across Different Magnet Materials
Different magnetic materials use distinct grading systems. While neodymium magnets follow an N-grade system (e.g., N35, N52), samarium cobalt (SmCo) magnets are categorized based on their alloy composition, such as SmCo5 or Sm2Co17. Ferrite magnets, on the other hand, are graded numerically (e.g., C5, C8) and offer lower magnetic strength but superior cost-effectiveness.
Common Magnet Materials and Their Grading Systems
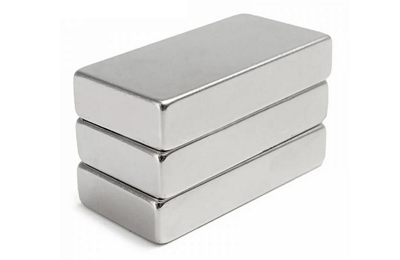
Neodymium (NdFeB) Magnets: Strength and Temperature Considerations
Neodymium magnets are the strongest commercially available permanent magnets, with energy products ranging from N35 to N55. However, they are highly susceptible to heat and corrosion, necessitating protective coatings and temperature-specific grades like N42SH for high-temperature applications.
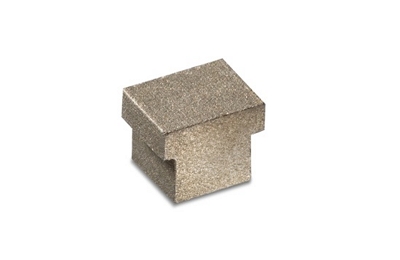
Samarium Cobalt (SmCo) Magnets: High-Temperature Stability and Corrosion Resistance
SmCo magnets offer superior thermal resistance, with operational limits reaching 350°C (662°F). Their coercivity makes them ideal for aerospace, defense, and high-performance motor applications. Unlike neodymium, they do not require protective coatings due to their corrosion-resistant nature.
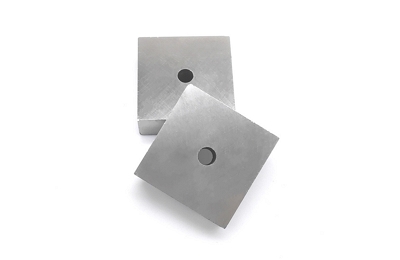
Alnico Magnets: Legacy Performance and Customizable Shapes
Alnico magnets, composed of aluminum, nickel, and cobalt, boast excellent thermal stability and can operate in temperatures exceeding 500°C (932°F). While they have lower magnetic strength than neodymium or SmCo magnets, their ability to be cast into intricate shapes makes them valuable in specialized applications such as sensors and instrumentation.
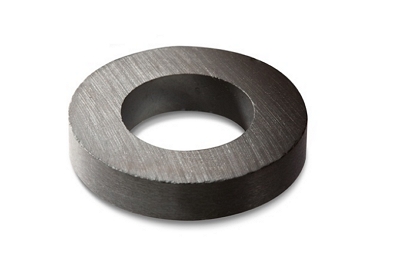
Ferrite (Ceramic) Magnets: Cost-Effective and Widely Used Solutions
Ferrite magnets provide an economical alternative with decent magnetic performance. Despite their lower energy product, their affordability and resistance to demagnetization make them ideal for loudspeakers, motors, and industrial equipment.
Understanding Key Magnet Properties in Magnet Tables
Remanence (Br): Measuring the Magnet's Retained Strength
Remanence, denoted as Br, quantifies a magnet's residual field strength post-magnetization. Higher values signify greater holding capacity when measured in Tesla or Gauss. Magnet tables list Br to aid in assessing suitability for static applications, such as clamps or separators.
Coercivity (Hc): Resistance to Demagnetization
Coercivity (Hc) reflects a magnet's tenacity against external magnetic fields or heat-induced losses. High Hc values, often seen in samarium cobalt, ensure reliability in dynamic settings. Tables juxtapose intrinsic (Hcj) and standard (Hcb) coercivity, offering a granular view of resilience.
Maximum Energy Product (BHmax): Defining Overall Magnetic Performance
The maximum energy product, or BHmax, integrates remanence and coercivity into a single metric of magnetic efficiency. Expressed in MGOe, it dictates a magnet's work capacity. Magnet tables highlight BHmax to guide selections where power density is paramount.
Temperature Resistance and Curie Temperature: How Heat Affects Magnet Strength
Temperature sensitivity varies across magnet types. The Curie temperature marks the threshold beyond which a magnet loses its magnetic properties. For example, neodymium magnets typically have a Curie temperature of 310-370°C (590-700°F), while SmCo magnets can exceed 800°C (1472°F).
Applications and Use Cases
How to Choose the Right Magnet Grade for Industrial Applications
Application-specific considerations include:
• Motors and Generators – Require high coercivity to withstand external magnetic fields.
• Medical Devices – Favor SmCo or coated neodymium for corrosion resistance.
• Electronics – Utilize ferrite magnets for affordability and stability.
Trade-Offs Between Magnetic Strength, Temperature Resistance, and Cost
Selecting the correct grade involves balancing power with environmental constraints and budget limitations.
Why Higher Grades Aren't Always the Best Choice
Higher-grade magnets can be more brittle, expensive, or less temperature-stable. Practical selection depends on application-specific performance, not just raw magnetic strength.
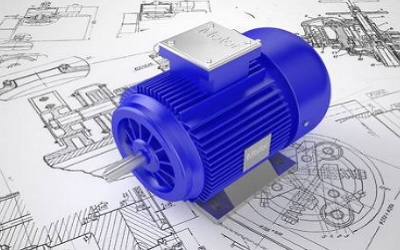
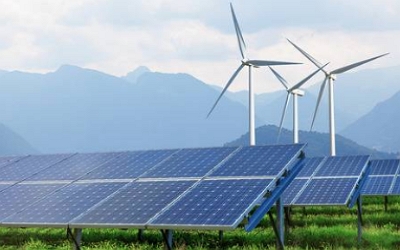
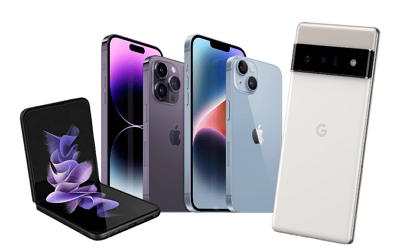
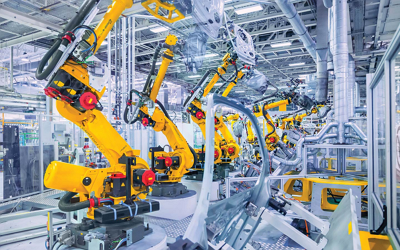
Interpreting and Using Magnet Tables for Selection
How to Read a Magnet Table: Key Parameters and Their Meanings
Magnet tables array parameters like Br, Hc, and BHmax across grades and materials. Annotations clarify units and conditions (e.g., 20°C testing). Proficiency in reading these tables hinges on understanding each metric's real-world implications.
Comparing Different Magnet Grades for Optimal Performance
Side-by-side comparisons in tables expose nuances—say, N42 versus N42SH in thermal stability. This facilitates pinpointing the grade that harmonizes a given task's strength, durability, and cost.
Common Mistakes to Avoid When Selecting a Magnet from a Table
Misinterpretation of coercivity vs. operating conditions, overlooking temperature effects, and over-prioritizing strength or misinterpreting BHmax as the sole criterion can derail selections. Ignoring material-specific quirks, like neodymium's corrosion propensity and compound errors. Vigilance with table data averts such pitfalls.
Advanced Considerations for Engineers and Technicians
Coating and Plating Options: Enhancing Performance and Longevity
Coatings like nickel or epoxy bolster corrosion resistance and durability, particularly for neodymium. Magnet tables may note compatible options, influencing grade choice in harsh environments.
Understanding Magnetization Direction and Its Impact on Functionality
Magnetization orientation—axial, diametric, or radial—shapes field distribution. Tables occasionally specify standard directions, guiding engineers in aligning magnets with mechanical designs.
Custom Magnet Design: When Standard Grades and Tables Aren't Enough
Tailored magnetic solutions—such as hybrid materials and composite configurations—offer performance advantages over off-the-shelf grades for niche applications.
Conclusion
Recap of Key Takeaways on Magnet Grades and Tables
Understanding magnet grades and tables simplifies the selection process, ensuring optimal performance for specific applications. Engineers and procurement specialists can make informed decisions when choosing the right magnet by considering factors such as magnetic strength, coercivity, temperature resistance, and cost-effectiveness.
Final Tips for Choosing the Right Magnet for Your Needs
Selecting a magnet goes beyond just picking the most potent option. It requires balancing performance with environmental conditions, operational demands, and budget constraints. Evaluating magnet properties through tables and grade classifications allows for a precise match to the application's requirements.
Get in Touch with Us
If you need assistance selecting the right magnet for your application or have specific requirements for custom magnetic solutions, our team is here to help. With extensive experience in the industry, we provide professional support, technical expertise, and high-quality permanent magnet products. Contact us today to discuss your needs and discover the best solutions for your business.
Post time: Mar-04-2025