Introduction
Magnets are more than just fridge decorations or science fair curiosities - they're powerful tools in engineering design. From electric motors to magnetic locks, engineers harness their unique properties to solve real-world problems. But designing with magnets isn't as simple as sticking two poles together and calling it a day. It requires a blend of physics, material science, and practical know-how. In this post, we'll share actionable tips to help you design effectively with magnets, whether you're a seasoned engineer or just dipping your toes into the magnetic field (pun intended). Let's dive in.
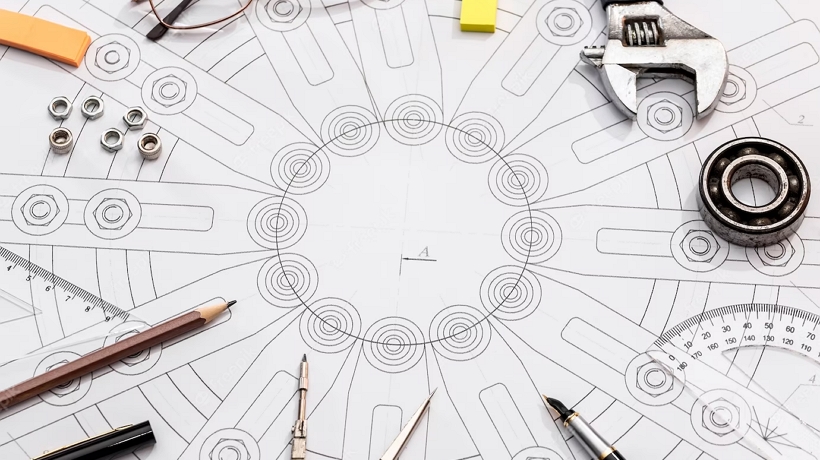
Understand Magnet Basics Before You Start
First things first: know your magnets. Permanent magnets, like neodymium (NdFeB) or samarium-cobalt (SmCo), generate a constant magnetic field without external power. Electromagnets, on the other hand, rely on electric current to create a field, offering control but requiring energy. Temporary magnets, such as soft iron, only exhibit magnetism when exposed to a field.
Each type has its strengths. Neodymium magnets pack a punch in small packages-think high torque in compact motors-while electromagnets shine in applications needing on-off functionality, like cranes or MRI machines. Before sketching your design, ask: What's the job? Do you need strength, switchability, or heat resistance? For instance, SmCo magnets hold up better at high temperatures, making them ideal for aerospace sensors, while neodymium's raw power suits consumer electronics.
Pro tip: Check the magnet's maximum energy product (BHmax)-a measure of its magnetic strength-and its coercivity, which tells you how well it resists demagnetization. These specs guide your choice and prevent costly redesigns.
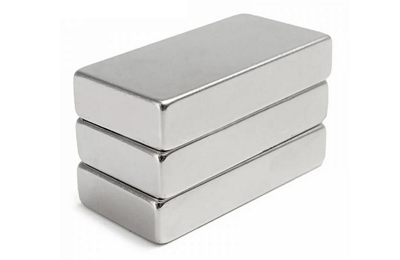
Neodymium Magnets
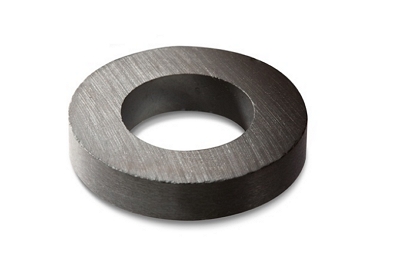
Ferrite Magnets
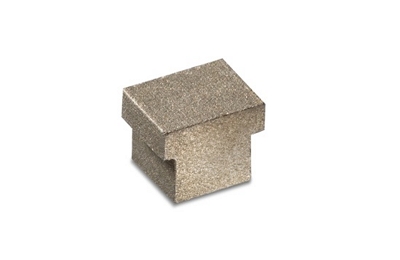
Samarium Cobalt Magnets
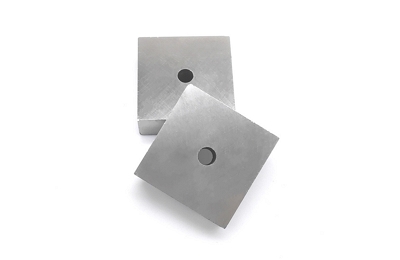
Alnico Magnets
The Role of Magnets in Everyday Life and Industrial Applications
Magnets are ubiquitous in modern society. In everyday applications, they are found in household items such as speakers, electric motors, and door latches. In industrial settings, they play a pivotal role in wind turbines, medical imaging devices, and precision engineering. Understanding the differences between regular and neodymium magnets ensures that industries can maximize efficiency and longevity in their applications.
Factor in Magnetic Fields and Interactions
Magnets don't work in isolation. Their fields interact with nearby materials and other magnets, often unexpectedly. Picture this: You're designing a magnetic latch for a cabinet. You position two neodymium magnets to attract each other, but nearby steel hinges distort the field, weakening the hold. That's a real headache if the latch fails mid-use.
To avoid this, map the magnetic field early. Tools like finite element analysis (FEA) software (e.g. ANSYS) simulate field lines and reveal interference. Suppose software isn't an option; prototype with a simple compass or iron filings to visualize the field. Keep ferromagnetic materials-like iron or nickel-at a safe distance unless they're part of the design. For example, you'd channel the field through a steel rotor in a motor, but in a sensor, stray steel could throw off readings.
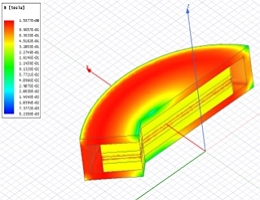
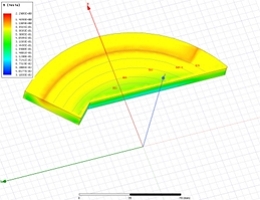
Optimize Magnet Placement and Orientation
Placement matters. A magnet's force drops off with distance-roughly following an inverse-square law for point sources-so position magnets as close as possible to their target without compromising safety or mechanics. Orientation is equally critical. Align the poles (north and south) to maximize attraction or repulsion, depending on your goal.
Take a magnetic coupling in a pump. Two-disc magnets, one on the motor shaft and one on the impeller, transfer torque without physical contact. If the poles are misaligned, you lose efficiency and the pump struggles. Test alignments with a mock-up: rotate one magnet and measure the force with a spring scale. Small tweaks can double the performance.
Another trick: Stack magnets to boost strength. Two neodymium discs stacked north-to-south amplify the field but watch out-stack too many, and you hit diminishing returns due to saturation. Experiment to find the sweet spot.
Account for Environmental Stressors
Magnets aren't invincible. Temperature, corrosion, and mechanical shock can degrade performance. Neodymium magnets, for all their strength, lose magnetism above 80°C (176°F) unless you specify a high-temp grade (e.g., N42SH, good to 150°C). SmCo or Alnico magnets handle heat better but cost more. Check your operating environment and pick accordingly.
Corrosion is another gotcha. Neodymium magnets rust easily without a coating like nickel or epoxy. An unprotected magnet could crumble in months in a humid setting-like a marine application. I've seen engineers salvage designs by adding a sealed enclosure, but it's smarter to coat the magnet upfront.
Shock can also demagnetize or crack brittle magnets. Secure magnets with adhesive (e.g., epoxy) or a mechanical clamp in a vibrating machine. A robotics team once lost a gripper's hold because a neodymium magnet shattered under impact. A rubber cushion solved it.
Balance Cost and Performance
Magnets can break your budget if you're not careful. Neodymium magnets offer the best bang for your buck, with prices around $0.10–$1 per gram, depending on size and grade. SmCo costs triple that, and custom shapes jack up the price further. Before splurging, ask: Does the design need this magnet? A weaker ferrite magnet might suffice for a low-force latch, saving cash without sacrificing function.
Standard sizes are cheaper than custom cuts, so browse our catalogs early. Consider assembling smaller magnets into a composite if you need an odd shape. One engineer I know built a ring magnet from arc segments half the cost of a custom mold.
Prototype and Test Aggressively
Theory's great, but magnets love to surprise you. Build a prototype and test it under real conditions. Measure force with a pull tester, check field strength with a Gaussmeter, and run it through temperature cycles. A medical device team once designed a magnetic valve, only to find it stuck in humid conditions-testing revealed corrosion they hadn't anticipated.
Iterate based on results. Swap magnet grades, tweak spacing, or add shielding to redirect stray fields. Document what works; it'll save time on the next project.
Safety First: Handle with Care
Magnets aren't toys. A strong neodymium magnet can snap fingers or erase a credit card's stripe from a foot away. Wear gloves and keep magnets apart during assembly-use spacers like wood or plastic. In a factory I visited, a worker dropped two 2-inch magnets that collided and shattered, spraying shards. A simple jig could've prevented it.
Also, shield electronics. A magnet near a pacemaker or hard drive spells trouble-design with clearance or magnetic shielding in mind, especially for consumer products.
Case Study: Magnetic Door Lock
Let's tie this together with a practical example. Imagine designing a magnetic lock for a security door. You pick a neodymium magnet (N52 grade, 50 lb pull force) for its strength and size. You place it in the door frame, with a steel plate on the door, aligning poles for maximum attraction. FEA shows the field clears nearby wiring-no interference. As it's an outdoor setup, you coat the magnet in nickel for corrosion resistance and secure it with epoxy to handle slams.
Testing reveals a flaw: at 80°C, the force dips slightly due to heat. You upgrade to an N42SH grade, test again, and it holds firm. The cost stays under $20 per unit, and the lock passes a 1,000-cycle test. Success.
Wrapping Up
Designing with magnets blends science and art. Pick the right type, map the field, optimize placement, and test relentlessly. Factor in environment and cost, and always prioritize safety. With these tips, you'll turn magnetic challenges into engineering wins.
Ready to magnetize your next project? Check out my related posts on [Magnets Selection Guide] for more insights.
Post time: Mar-19-2025