Permanent magnets are fundamental components across various engineering disciplines, from high-efficiency motors and precise sensors to sophisticated automation systems. While the inherent properties of permanent magnet materials dictate their potential, the magnetic circuit design truly unlocks their performance in practical applications. Effective magnetic circuit design is paramount to maximizing flux utilization, directing magnetic fields, and achieving desired performance characteristics. This blog post provides a technical overview of standard magnetic circuit designs employed in permanent magnet products, offering insights into their principles, advantages, limitations, and typical applications. At AIC Magnetics, we leverage our deep expertise in magnetic circuit design to engineer optimized solutions that meet the evolving demands of modern industries.
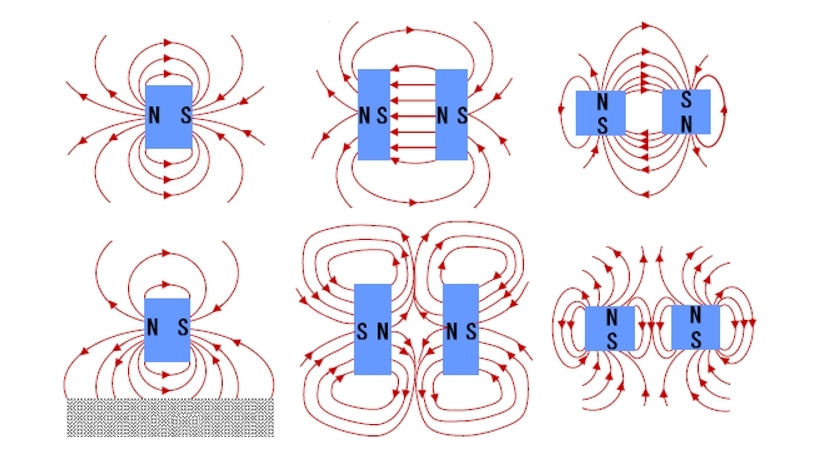
1. Closed Magnetic Circuits
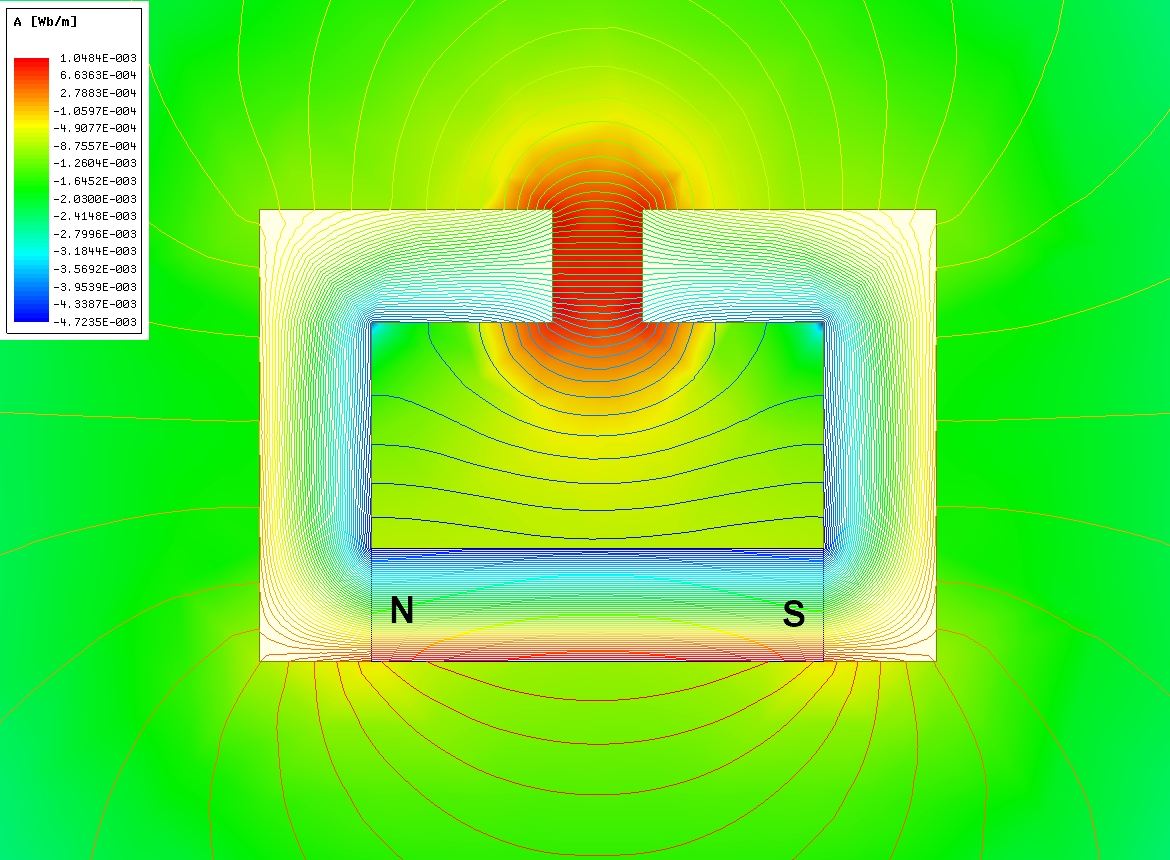
• Basic Principle: Closed magnetic circuits are designed to confine the magnetic flux within a high-permeability path, minimizing leakage and maximizing flux density in a defined air gap. Analogous to electric circuits, where current flows in a closed loop, magnetic flux in a closed circuit predominantly flows within ferromagnetic materials, which offer low magnetic reluctance.
• Structure: Typically, closed magnetic circuits utilize soft ferromagnetic materials like iron, steel, or ferrite to create a closed loop path for the magnetic flux. Permanent magnets are placed within this loop, often with pole pieces concentrating flux at the air gap. Standard configurations include U-shaped cores, C-shaped cores, and ring cores.
2. Open Magnetic Circuits
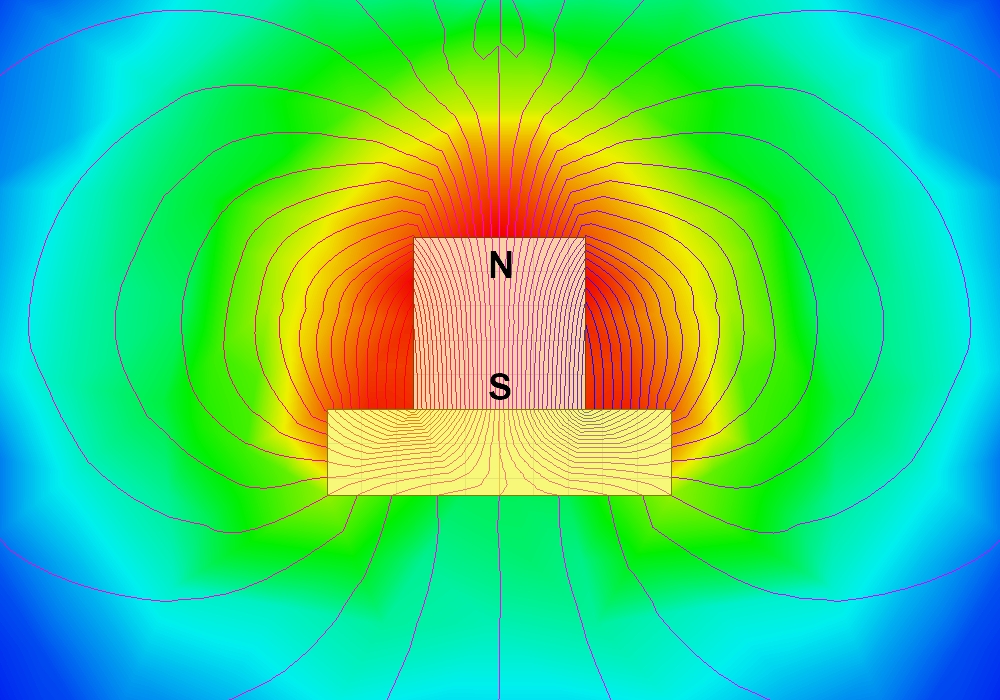
• Basic Principle: Open magnetic circuits, in contrast, do not entirely confine the magnetic flux within ferromagnetic materials. A significant portion of the magnetic flux path involves air with high magnetic reluctance.
• Structure: Open magnetic circuits typically consist of permanent magnets used in isolation or with simple pole pieces without a complete ferromagnetic return path. Examples include rod, block, and horseshoe magnets without a ferromagnetic keeper.
3. Hybrid Magnetic Circuits
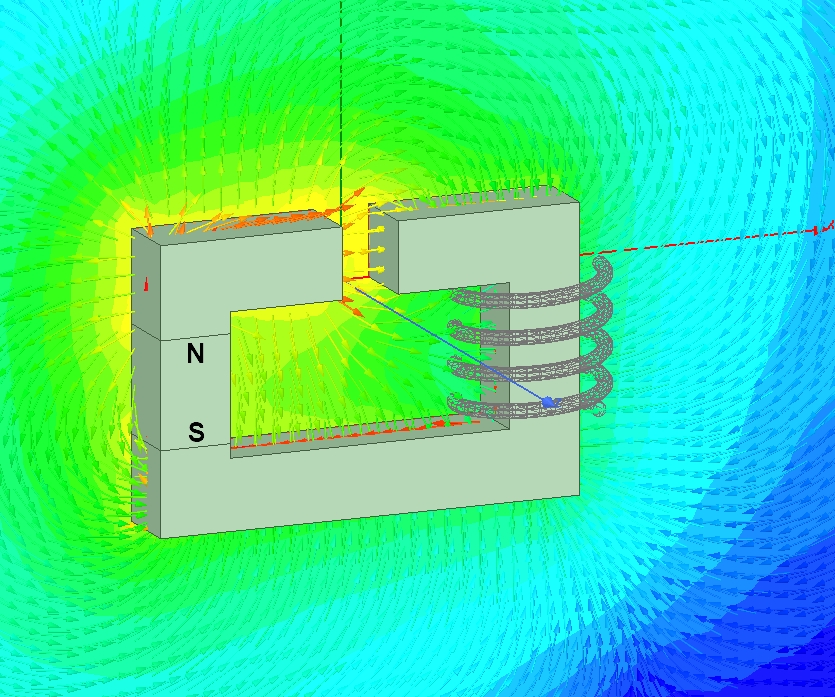
Basic Principle: Hybrid magnetic circuits combine the advantages of both permanent magnets and soft ferromagnetic materials (and sometimes electromagnetic coils) to achieve optimized magnetic performance. They strategically use ferromagnetic materials to shape and direct the magnetic flux generated by permanent magnets.
Structure: Hybrid circuits incorporate permanent magnets as the primary magnetic field source and utilize ferromagnetic components to tailor the field distribution, enhance flux density in specific regions, or provide flux paths. These designs can range from relatively simple modifications of closed or open circuits to highly complex configurations. Some hybrid designs also incorporate electromagnetic coils to allow for field control or modulation, creating hybrid excitation systems.
4. Special Magnetic Circuits
• Basic Principle: This category encompasses advanced and specialized magnetic circuit designs beyond the basic closed, open, and hybrid configurations to achieve unique magnetic field characteristics. Examples include Halbach arrays, magnetic focusing structures, and magnetic concentrating structures. These designs often utilize specific magnet arrangements or geometries to manipulate magnetic fields innovatively.
• Structure and Examples:
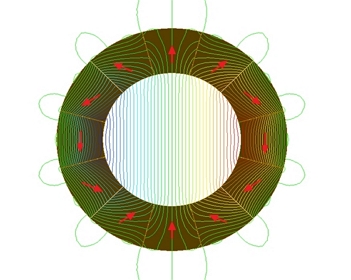
Halbach Arrays
As detailed in our previous blog post about Halbach Arrays, Halbach arrays are a unique arrangement of magnets designed to concentrate magnetic flux on one side while canceling it on the other. They achieve this through a spatially rotating pattern of magnetization.
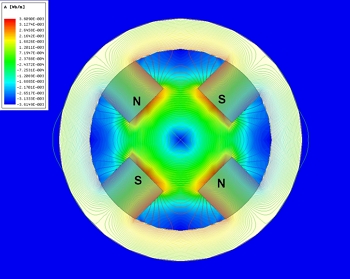
Magnetic Focusing Structures
These designs aim to focus magnetic flux into a small, defined area to achieve very high flux densities in that region. They often employ shaped ferromagnetic pole pieces and strategically placed permanent magnets. Examples include magnetic lenses for particle beam focusing and specialized magnetic sensors.
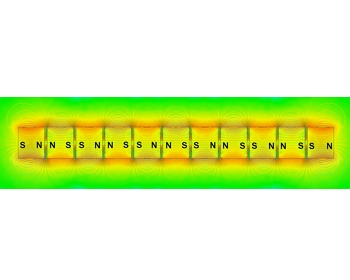
Magnetic Concentrating Structures
Similar to focusing structures, concentrating structures aim to increase flux density, but often over a larger area or volume. These may utilize tapered pole pieces or specific arrangements of magnets to "funnel" magnetic flux into the desired region. Magnetic chucks and types of magnetic couplings can employ concentrating structures.
AIC Magnetics Expertise in Magnetic Circuit Design
At AIC Magnetics, we possess a profound understanding of magnetic circuit principles and extensive experience designing and manufacturing various permanent magnet assemblies. Our engineering team combines expertise in magnet materials, magnetic simulation, and advanced manufacturing techniques to deliver optimized magnetic circuit solutions tailored to our clients' specific needs. We utilize state-of-the-art finite element analysis (FEA) software to model and simulate magnetic circuits, ensuring accurate performance prediction and design optimization. Our engineers can provide innovative and effective magnetic circuit designs, whether a simple open circuit, a complex hybrid system, or a specialized Halbach array. We are committed to partnering with our clients from initial concept to final production, providing comprehensive engineering support, and ensuring the success of their magnetic product applications.
Contact us today to discuss your specific magnetic circuit design requirements and discover how AIC Magnetics's expertise can help you achieve superior product performance and innovation. Let our experienced engineers partner with you to develop a customized magnetic solution that meets your unique application challenges.
Post time: Feb-13-2025